
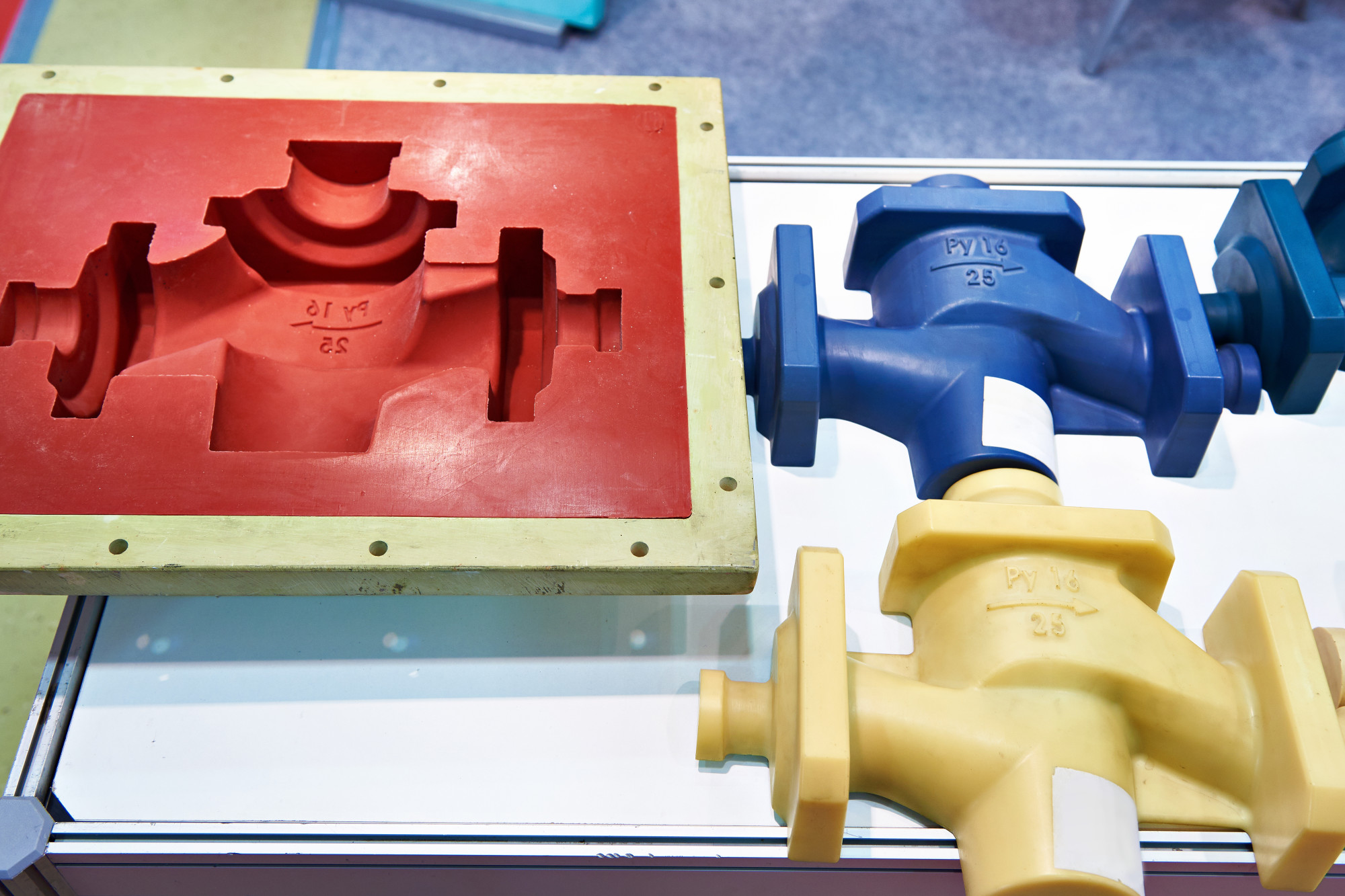
We also knew the part production required very high pressures and the molding machine would have to have a transducer in order to control actual cavity pressure of the resin. When we reviewed the tooling equipment and process it was apparent that the product could never maintain its specified dimensions because of an absence of underlying structural support in the mold. What Went Wrong: Tooling Equipment & Processĭuring our analysis, we also found that a deformation was occurring specifically in the direction of an out-of-tolerance condition. This meant part properties could not be attained, which is why the product was self-destructing within months. The molder was processing the resin cold, not realizing that the mold temperature had to be 360 degrees. The supplier did not realize they needed to process the resin, 50% carbon-filled PEEK (Polyetheretherketone), according to the exact requirements laid out in the resin manufacturer’s manual. The molding house was not experienced in dealing with complex engineering-grade resins. The supplier the company was using was a high volume molding house and had not developed the process correctly. When we arrived on-site we immediately identified that one of the major sources of failure was caused by an improper PEEK plastic injection molding process.
Peek plastic injection moulding series#
They told us that when they opened the parts on the assembly line to add them to the assembly what was supposed to be one part had deconstructed into many parts, resulting in a defective and unusable part.Īfter asking a series of technical troubleshooting questions, the company requested we visit the plant for an in-depth review and analysis of the molding process and tooling in place at their present supplier. The company called us and explained that their product was self-destructing within months of being received from the molding processor. BackgroundĪ military and aerospace hardware manufacturing company came to Plastic Molded Concepts with a product failure issue that persisted with their existing plastic injection manufacturer. This particular customer had a unique and complex PEEK plastic injection molding issue that its previous supplier was unable to solve: product self-destruction.įind out below how Plastic Molded Concepts solved and corrected this critical product failure issue in a military/aerospace component that was using PEEK plastic injection molding. Here at Plastic Molded Concepts, customers turn to us for solutions to complex plastic molding failures. Self-Destruction in Military/Aerospace Part Solved PEEK Plastic Injection Molding Military/Aerospace Case Study
